Spot weld or Mig Weld-Choose Carefully For Safety Reasons
Published by Giulio Valle in Informational · 29 September 2023
Tags: Spot, weld, or, Mig, Welding, Choose, Carefully, For, Safety
Tags: Spot, weld, or, Mig, Welding, Choose, Carefully, For, Safety
Spot weld or Mig Welding - Choose Carefully For Safety Reasons
The modern auto body shop is a place where vehicles are repaired, restored, and refinished after accidents or damages. The automotive repair industry has evolved significantly over the years, and with the advancement in technology, the equipment used in these facilities has also seen substantial transformations.
The spot welder is one such piece of equipment that has become a Must-Have for any modern auto body shop. In this comprehensive essay, we will explore the reasons why a spot welder is an indispensable tool in auto body repair.
FYI: The Pro Line Systems Research Team Has Discovered ThePercentage of auto body shops using Spot Welders vs. Mig Welders in 2023Spot Welders 70% - MIG Welders 30%Source: Collision Repair & Bodywork, 2023 Market Research Report
Spot Welders 70% - MIG Welders 30%
As you can see from the percentages above, spot welders are the most popular type of welder used in auto body shops in 2023. This is because spot welders are very good at welding thin sheets of metal together, which is what most car body panels are made of. Spot welders are also relatively easy to use and produce strong welds.
MIG welders are also used in auto body shops but are less used than spot welders. MIG welders are more versatile than spot welders, but they can be more difficult to use and produce weaker welds on thin sheets of metal. MIG welders are typically used for welding thicker pieces of metal, such as chassis frames and structural components.
It is important to note that the percentage of auto body shops using each type of welder may vary depending on the size of the shop and the types of vehicles it repairs. For example, larger shops that specialize in repairing heavily damaged vehicles may use more MIG welders.
We will cover various aspects, including the basics of spot welding, its advantages, safety considerations, and frequently asked questions.
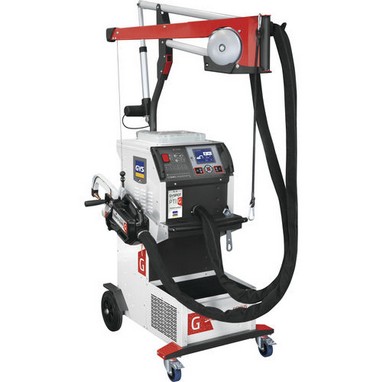
This is the GYSPOT PTI-G Smart spot welder, an example of the advanced welding machines available to the modern collision repair industry.
Amazing advanced technology and easy to-use interface make it to
the top of the list by many auto manufacturers including Mercedes.
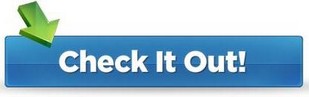
I. Understanding Spot Welding:
Spot welding is a welding technique used primarily in the automotive industry for joining two or more metal sheets together by creating a series of overlapping, short-welded spots. These welds are achieved by passing an electric current through two electrodes, which are pressed against the metal sheets. The heat generated at the contact points melts and fuses the metal sheets, creating a strong, safe, and nice factory-looking durable bond.
Let's Compare Spot Welding vs. Mig Welding And Why You Should Be Spot Welding
Key Components of a Spot Welder:
Electrodes:
These are the metal tips that come into direct contact with the workpieces and conduct the electric current to the electrode tips.
Transformer:
The transformer converts the input voltage to a lower, controllable welding voltage.
Control Panel:
This interface allows the operator to set various parameters such as welding power, time, and squeeze pressure. All these parameters are very important, especially on today's highly advanced steels.
Cooling System:
Spot welders generate significant heat during the welding process, so a liquid cooling system is essential to prevent overheating and maintain optimal performance and best cycle time.
II. Advantages of Spot Welders in Auto Body Shops:
A spot welder offers several advantages that make it an indispensable Must-Have tool in auto body shops:
Strength and Durability:
Spot welding creates welds that are incredibly strong and durable, ensuring the structural integrity of the repaired vehicle.
Speed and Efficiency:
Spot welding is a fast process, allowing technicians to complete repairs quickly and reduce downtime for customers. The short concentrated current if set up correctly, eliminates any degradation of the material being fused.
Precise Control:
Modern spot welders come with advanced control panels that allow operators to fine-tune welding parameters, ensuring consistent, safe, and high-quality factory-looking welds.
Reduced Heat Affected Zone (HAZ): This Is Critical. Unlike other welding methods, IE: Mig / Mag, etc.
spot welding minimizes the HAZ, reducing the risk of warping or distortion and compromising the integrity
of the metal.
Material Compatibility:
Spot welding can be used with a wide range of metals commonly found in automotive construction, including many variations of AHSS steel.
III. Safety Considerations in Spot Welding:
Safety is paramount in any auto body repair shop, and the use of spot welders is no exception. Here are the key safety considerations when working with spot welders:
Personal Protective Equipment (PPE):
- Welders should wear appropriate PPE, including gloves, flame-resistant clothing, and safety glasses.
Ventilation:
- Adequate ventilation is essential to remove fumes produced during welding. This ensures a safe and breathable working environment.
Fire Safety:
- Auto body shops should have fire safety measures in place, including fire extinguishers, fire blankets, and a designated safe area for welding.
Electrical Safety:
- Inspect and maintain welding equipment regularly to prevent electrical hazards. Cords and plugs should be in good condition.
Training and Certification:
- Technicians operating spot welders should receive proper training and certification to ensure they understand the equipment and safety procedures. ICAR classes are a good source of training.
Positioning and Workspace:
- Maintain a clean and clutter-free workspace to prevent tripping hazards. Ensure that the vehicle is securely positioned during welding to prevent accidents.
- FYI; It is always a good procedure to disconnect the vehicle's battery to prevent harming sensitive circuits and micro-processors located throughout the vehicle.
Material Compatibility:
- Shop owners and technicians must understand the specific requirements for welding different types of metals, as improper welding on certain materials can lead to safety hazards.
IV. Frequently Asked Questions (FAQs):
What types of vehicles can be repaired using a spot welder?
Spot welders are versatile and can be used to repair a wide range of vehicles, including cars, trucks, motorcycles, and even some larger vehicles like buses and recreational vehicles.
Can spot welding be used on aluminum vehicles?
Yes, spot welding can be used on aluminum vehicles. Mostly this is done on the vehicle assembly line. The robotic welders that can perform aluminum spot welds are extremely expensive and not practical for the common shop.
However, aluminum spot welding typically requires specialized equipment and techniques due to aluminum's unique properties. Currently, there are no portable aluminum spot welders for auto body shops.
In these cases, auto manufacturers are moving to self-piercing rivets and bonding material for vehicle assembly with outstanding results. Ford, Lincoln, Tesla, Mini Cooper, and Freightliner, to name just a few.
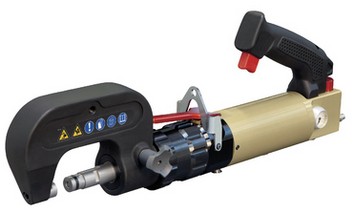
For Example:
Check Out Our #1 Selling Riveter The GYSPRESS 10T.
Amazing Performance And Price
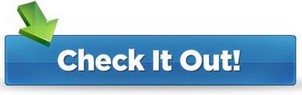
Are there different types of spot welders?
Yes, there are various types of spot welders, including Smart welders which automatically set up the welding parameters for the particular type of steel, and thickness of material. Also handheld, portable, and stationary models. The choice of spot welder depends on the specific needs and scale of the auto body shop.
How can I ensure the quality of spot welds?
Quality spot welds depend on factors such as welding current, pressure, timing, and electrode condition. Regular maintenance of the spot welder and proper training for technicians are crucial for achieving consistent weld quality.
Interested in learning more?
Go to our special Blog- 5 Essentials To Complete Before Spot Welding A Vehicle
What are some common problems in spot welding, and how can they be resolved?
Common spot welding issues include weak or incomplete welds, electrode wear, and overheating. These problems can often be resolved through adjustments to welding parameters, electrode replacement, or equipment maintenance. Yes, your spot welder needs maintenance!
Is spot welding environmentally friendly?
Spot welding is generally considered an environmentally friendly welding method. It produces minimal fumes and does not typically require the use of harmful chemicals.
Are there any regulations or standards for spot welding in auto body shops?
Yes, there are industry standards and regulations that govern welding processes in auto body shops. These standards ensure safety and quality in automotive repairs. Compliance with these standards is essential.
Mig / Mag Welders
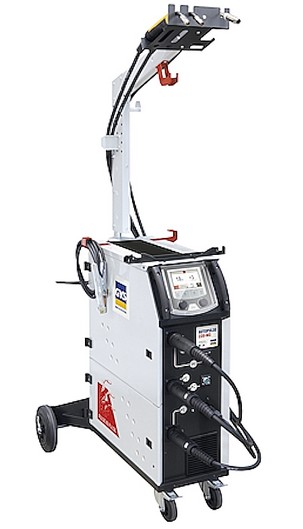
Here is an example of a very popular industry-approved Mig
welder - The GYS - Autopulse 220-M3
This is a 3-drive machine with all the latest technology for
Aluminum, Steel, And Silicon Bronze.
Learn more about this amazing wire feed machine on our web page
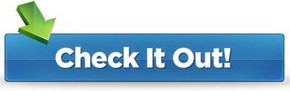
If I use a mig welder instead of a spot welder could this be a safety problem and why?
Using a MIG (Metal Inert Gas) welder instead of a spot welder in an auto body shop can indeed present safety problems and may not be suitable for certain applications. Here are several reasons why:
Structural Integrity:
One of the primary concerns with using a MIG welder in place of a spot welder is the potential impact on the structural integrity of the vehicle. Spot welding creates localized, strong, and precise welds that mimic the factory welds used in vehicle construction. MIG welding, on the other hand, can produce larger and less controlled welds, which may compromise the structural integrity of the repaired area and therefore create a safety concern.
Heat-Affected Zone (HAZ):
MIG welding generates significantly more heat compared to spot welding. This can lead to a larger heat-affected zone in the surrounding metal, potentially causing warping, distortion, or weakening of the panel being repaired. In contrast, spot welding minimizes the HAZ.
FYI: If A Mig / Mag Machine Must Be Used On Thin Sheets Of AHSS Steel Or Aluminum,
Be sure your machine utilizes Double Pulse Technology and can lower the power, and wire feed to very low settings. Keep in mind, that the HAZ needs to be kept low to avoid material damage from excessive heat.
Aesthetic Concerns:
MIG welds tend to be more visible and may require more extensive finishing work to achieve a smooth and aesthetically pleasing appearance. This can be problematic, especially in auto body repairs where maintaining the vehicle's original appearance is crucial.
Material Compatibility:
Some auto body panels are made of materials like aluminum, which require specialized welding techniques and equipment. MIG welding, if not adapted for aluminum, can result in weak and brittle welds on these materials compromising safety. FYI: Whatever Mig welder you choose, be sure it is one designed for automotive use and not for industrial use as these won't be able to weld thinner metals without overheating the material.
Inconsistent Weld Quality:
MIG welding requires a high degree of skill and precision to consistently produce strong and safe welds. Inexperienced welders may create weak or improper welds, leading to safety issues down the line.
Corrosion Concerns:
MIG welding can introduce additional concerns regarding corrosion, especially if the welding is not done correctly or if proper post-welding treatments (e.g., coating or sealing) are not applied. Spot welds generally create fewer points of potential corrosion.
Safety Hazards:
The use of MIG welding equipment introduces additional safety hazards, such as the risk of electrical shock, exposure to welding fumes, and fire hazards. Proper safety measures, including personal protective equipment and ventilation, must be in place when using MIG welders.
Regulatory Compliance: Always Check And Follow The OEM Recommended Procedures.
Auto body shops are often subject to industry standards and regulations that require specific welding methods for structural repairs. Using a MIG / Mag welder when spot welding is specified may lead to non-compliance with these standards, potentially resulting in legal and liability issues.
Final Summary:
While MIG welding is a valuable and versatile welding process, it may not be the best choice for all auto body repair applications, particularly when it comes to structural integrity and safety concerns.
Spot welding remains the preferred method for many auto body repairs because of its ability to create strong, precise, and aesthetically pleasing welds while minimizing potential safety risks associated with MIG welding.
The choice between spot welding and MIG welding should be made based on the specific repair requirements and adherence to safety and regulatory standards.
So, as you have learned, Spot welding is the first choice and most used method in the modern
collision repair facility because of the many good reasons we've mentioned in this article.
So What Do You Think?
Please leave a comment below, we'd like to see it.
Are you looking for an Auto Body Repair Equipment Supplier with an excellent reputation,
products, and pricing? Pro Line Systems International is the place. Click here to get a quote.
FYI: Hey, Curious about Giulio Valle, the Authoritative Author, and creator of this Blog and the
Pro Line Systems Website? Check Out Giulio's Interesting Brief Biography Here
